Validation
Performing validation solutions for technologies to demonstrate benefits
To reach a certain maturity technologies need to be validated. Experimental validation of either prototypes, demonstrators or with regard to final product validation in a realistic environment is a key aspect for maturing developed solutions.
IBK supports these validation steps on all levels:
- Technology validation/ Product validation using wind-tunnel models
- Model identification using flight/ ground tests
- Component/ Sub-system test
- Proof of concepts under lab-conditions
We provide the validation strategy for specific developments and are able to manage and perform all relevant steps necessary to achieve high technical readiness levels for new technologies.
Wind-Tunnel Tests
IBK has demonstrated a strong background which was developed in particular due to a large number of successful test activities in the JTI-Cleansky 1 program. Within this huge European research environment IBK supported several validation campaigns, in particular test-campaigns in which technologies were analysed in an environment that enables realistic assessment.
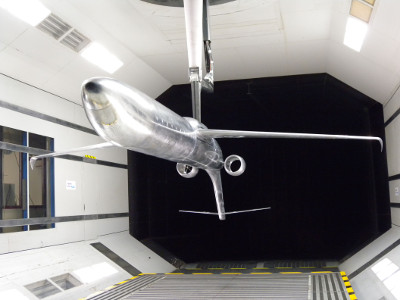
Core activities in this regard are wind-tunnel test activities. IBK has the competence to design wind-tunnel models for all wind-tunnels currently operated. These models can be either component models (wing-only), half-models or full models. So far models including powered engine simulations have been developed as well as dynamically scaled wind-tunnel models for Load-Control and Alleviation purposes.
Due to the strong background in aerodynamics and structural mechanics IBK is able to design these models including the full stiffness/ strength analysis and aerodynamic assessment under WT-conditions, if necessary. Safety and efficiency are key in the wind-tunnel.
Over the years IBK has established a network of manufacturers we are cooperating with. In parallel to the design activities IBK is therefore able to manage the manufacturing, including acceptance tests and all necessary preparations to ensure robust testing scenarios. A well established contact to relevant European wind-tunnel operators is existing that ensures direct communications to quickly resolve open questions.
Beyond activties with regard to wind-tunnels IBK has supported (and is still supporting) projects in which a part of the activties are related to tests.
Model identification
Model identification tests are performed in order to validate virtual models used for validation. Examples for these kind of tests can be ground-vibration tests, test to identify the aerodynamic behaviour or tests to identify mass and mass-moments of inertia.
As an example a test for identifying the mass moment of inertia is given here. For this test the aircraft is fixed in a way that rotation only in the predefined axis of interest is possible. By exciting an oscillating rotation about the fixation and measuring the dynamic motion, IBK is able to calculate the mass moment of inertia properties of the aircraft.
The dynamic motion of the aircraft is recorded by a stand-alone inertia measurement unit (IMU), which can be easily equipped into the aircraft. The IMU measurements recorded, in terms of the accelerations, rotation rates, and attitude angles, can be accessed remotely and allow a direct evaluation of measured values.
IBK has gained experience and expertise in performing highly specialized tests in the past and with current projects. The individual mounting of the aircraft as well as the special test setup is designed by IBK and special mounting parts can be manufactured by our established network of manufacturers.
Component/ Sub-Component Tests
In Aeronautics component and sub-component tests are performed in order to optimise testing activities with regard to effort and output. IBK is not only able to provide support to design activities but is also able to design and validate whole components for complex setups.
As an example the video shows the demonstration of an actuated flap in relevant conditions in an industrial wind-tunnel. The use of actuated flaps in the wind-tunnel reduces the time to change the setting by also enabling continuous and flexible positioning of movable surfaces with the consequent enhancement of test productivity.
Within the project POLITE, IBK developed this solution and was able to demonstrate its maturity inside the RUAG-LWTE (Large Wind-tunnel Emmen) during a test-campaign.
Proof-of-concept
Proof-of-concept often includes tests on a localised, representative structure on lab-level that helps to understand if a certain effect is reproduced as originally planned. Proof-of-concept tests also can be used to understand the complexity and interfaces with other elements in a better way. IBK has performed these kind of tests in various projects in the internal facility, often making use of Rapid-Prototyping infrastructure within the IBK-network to quickly establish and tests solutions.
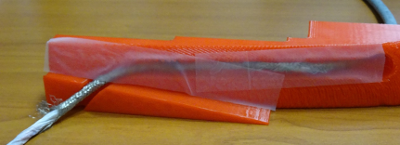
As an example the wire bending demonstrator is shown. For wind-tunnels models space is often very restricted, in particular in areas of interest for WT-Models (e.g. wings, high-lift devies). In the current situation a wire needed to send an encoder signal had to be routed in a very complex way. Questions about assembly and accessability came up. By producing a small demonstrator the concept could be tests and proofed.
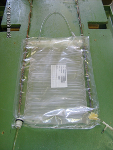
As a second example a proof-of-concept for a portable cooling system used to support humans after a stroke was tested. Important questions were wether the mechanism to start the cooling process is robust and if the cooling effect stays available for a certain time.