T-WING
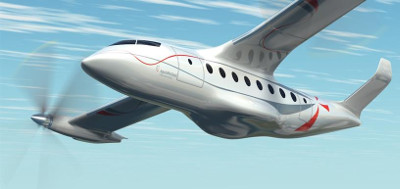
The T-WING project is aimed at developing, manufacturing, testing, and qualifying an Innovative Composite Wing for the Technology Demonstrator (TD) of the Next Generation Civil Tilt Rotor (NGCTR), performing at the same time studies on the scalability potential of the proposed solutions for the exploitation of the technologies on the full-scale aircraft.
As integral part of the whole activity, the Consortium will work in close cooperation with LEONARDO Helicopter Division (LHD) in all the assembly and installation phases into the NGCTR prototype as well as during vehicle ground and flight testing.
The wing is the main subsystems of most flying vehicle. The need to design a wing with high performance in terms of efficiency, drag, improved life and reduced weight and life cycle cost, poses many challenges to the designers. Additional complexity is due to the unique character of a tiltrotor aircraft, indeed the presence of tilting motors installed at wing tips introduces very uncommon load scenarios due to the possibility to fly as an airplane, land and take-off as a STOL aircraft (nacelle in intermediate configurations), and to land, take-off and hover as a helicopter. Indeed, during flight and approach operations, it can work in a set of different transitional configurations.
The presence of thrust forces at wing tips leads to increased spanwise bending moments, and large masses and rotating parts involved require optimized torsion and bending stiffness distributions to counteract whirl flutter instabilities. All these peculiar aspects lead to unique stiffness tailored wing architecture.
In addition, it is also a must of the concurrent engineering development cycle to control all the technical aspects including also environmental and maintenance issues related to the entire life of this peculiar product. These challenges can be faced only by employing advanced technologies and a strong multidisciplinary approach involving fields like: architecture and configuration, aeroelasticity and loads, design and analysis practice, materials and processes selection, production methods, tests and qualifications expertise, quality, safety & reliability engineering and airworthiness.
After a System Requirement Review, a preliminary system design activity and a technological innovation assessment, aeroelastic analyses are being performed to derive stiffness and inertia requirements as well as all the relevant flight and ground load cases useful to size the wing structure. The first proposed structural concepts are being conceived as a natural evolution of already flying solutions, designed, produced, certified and patented by a T-WING partner according to CS/FAR-25 Airworthiness Requirements.
The T-WING consortium is committed to perform all the design and analysis activities, by maximizing low weight and safety, technological and manufacturing efficiency criteria fully compliant with a flight condition approval plan (basis for flightworthiness are CS-25, CS-29 + special conditions) and LHD Requirements.
Special care is dedicated to the effective application of a set proposed innovative manufacturing technologies. With the aim to go beyond the state of the art, already partially developed innovative solutions with a high level of integration are being investigated, for lower complexity, weight and cost. Technology maturation activities on composite thermoplastics are investigated as well, with the addition of the application of Additive Layer Manufacturing (ALM) techniques for metallic secondary structures, for weight and waste reduction. The proposed innovative approach and solutions will be preliminary assessed and subsequently calibrated and validated by tests.
T-WING will therefore manufacture suitable sets of subcomponents for intermediate tests, three sets of wings including main fittings as well as suitable rigs, jigs and tools. The first two sets will be used for tests and qualification at component level: static tests (limit and ultimate), fatigue test, Ground Vibration Test (GVT, both in stand-alone configuration and after A/C installation), Crash Resistance Test (according to CS-29-952), bird strike, lightning, HIRF (High Intensity Radiated Fields), and functional tests are some of the tests foreseen for qualifying the T-WING system. The third set will be installed on the TD for ground and flight test campaigns. At the end of the project the TRL6 achievement will be verified.
In addition, T-WING is investigating and further developing specific topics in order to go “beyond the state of art” of the wing design practice, such as Aeroelastic Tailored Design and the Life Cycle Analysis in the Design Loop.
IBK supports CIRA (The Italian Aerospace Research Centre) in the Coordination of the project, performs all the aeroelastic and loads analysis in the perimeter of the project, performs the design of the load monitoring system, and support UNINA (the University of Naples) in the preparation and execution of Ground Vibration Tests.
The following partners contribute to T-Wing:
- CIRA à Coordination, preliminary design, support to aeroelastic analysis, support to technology development and qualification.
- MAGNAGHI à Wing Design and Analysis, Qualification Tests
- SALVER à Manufacturing and instrumentation for tests
- SSM à Support to the detail design, construction drawings and detail analysis; crash analysis
- UNINA à Preparation and execution of GVTs
- IBK à Support to Coordination, Aeroelasticity and Loads, design of load monitoring system, support to GVT
T-Wing startet 01.01.2018 and lasts for 72 months.
The T-WING project has received funding from the Clean Sky 2 Joint Undertaking under the European Union’s Horizon 2020 research and innovation programme under Grant Agreement FOR Members (GAM) No.807090.