ETRIOLLA
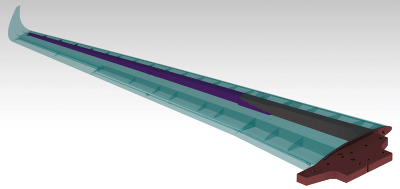
The scope of ETRIOLLA project is to design an elastic, natural laminar flow (NLF) wind tunnel model and test it in transonic and off design conditions, including the optimization of the load control and alleviation (LC&A)
According to the ACARE 2020 vision new aircraft generations shall be greener, cleaner and more efficient. A promising technology to reach these goals is the natural laminar flow (NLF) wing technology, where the air around the flying wing remains as long as possible (from leading edge to trailing edge) laminar (instead of being complete turbulent). As result drag and noise - induced by the wing - are reduced significant.
In order to get best possible test results, the RE number needs to be as high as possible. This can be achieved best with a big model (span in ETRIOLLA is ~5,60m which is equivalent to a scale of 1:3,05) and a test velocity in the wind tunnel in the order of cruise velocity (design condition).
Because the NLF is very sensitive to the shape and disturbances like steps, gaps and surface roughness, the model surface had to be very smooth with extraordinary high tolerances. Model deformations from aero loads were analyzed upfront, so that the target twist deformation over the span is met under test conditions with aero loads (hot shape). Therefore, the model design is characterized as an elastic model (jig shape is not the same like the hot shape).
Because wind tunnel test time is very expensive and a configuration change on such a large model is a challenging job, the ETRIOLLA model was designed with five independent, remote controlled movable devices, including real time sensing of position and force measurement on the flaps. To make sure that everything works as intended a flap demonstrator was build and the actuation was tested in the IBK LAB upfront – including the simulation of a bended and twisted wing and their effect on the hinges and the according friction changes.
Parallel and interacting with the WT model design, the wing was analyzed in terms of aerodynamic loads (in different configurations), deformations, structural and dynamic behavior.
Prior to the wind tunnel test a static load test and a ground vibration test (GVT) was performed by UOB in order to check the real model behavior and to assess possible risks during the WT test (flutter, stability (divergence)).
The model itself was tested in France in the ONERA S1 wind tunnel. The Laminar extend was made visible by the help of an infrared paint on the wing surface. As result the laminar flow in cruise conditions (MA 0,74) was almost 70% on the upper surface and ~30% on the lower surface – which is an extraordinarily good result. In the other part of the test campaign the LC&A device settings were checked and optimized.
All in all, ETRIOLLA was a success and which is proven with the project nomination for the “best project award” within the Clean Sky program. Within ETRIOLLA innovative techniques were successfully applied and the technical limits could be shifted a bit beyond common limits. Innovative approaches in ETRIOLLA are the elastic WT model design with remote controlled flaps and their real time position- and force measurement, the highly interactive and iterative connection between simulation and design (including the application of a genetic optimization algorithm), the big model size with their high tolerances and the simulation tools to predict the correct model behavior and model properties.
This success was not possible without a great team, and we want to express our thanks to the partners FOI (CFD simulation), UOB (static and dynamic simulations and tests), the manufacturer Eliglio Re Fraschini and the ONERA team. Last, but not least we want to thank also the IBK team for handling the challenging job of project coordination, WT model design and simulation (CFD, structural and dynamic design)
The following partners supported ETRIOLLA:
ETRIOLLA started 01/2013 and ended 12/2016. The project has received funding from the Clean Sky Joint Undertaking under grant agreement No. 323460.